Investments in Technology
and Training Strengthen Bangladesh’s Garment Industry
Orders plummeted at the start of the pandemic, and the drop in sales severely impacted Bangladesh’s ready-made garment industry. New technology and skills training for women workers can help factories remain competitive.
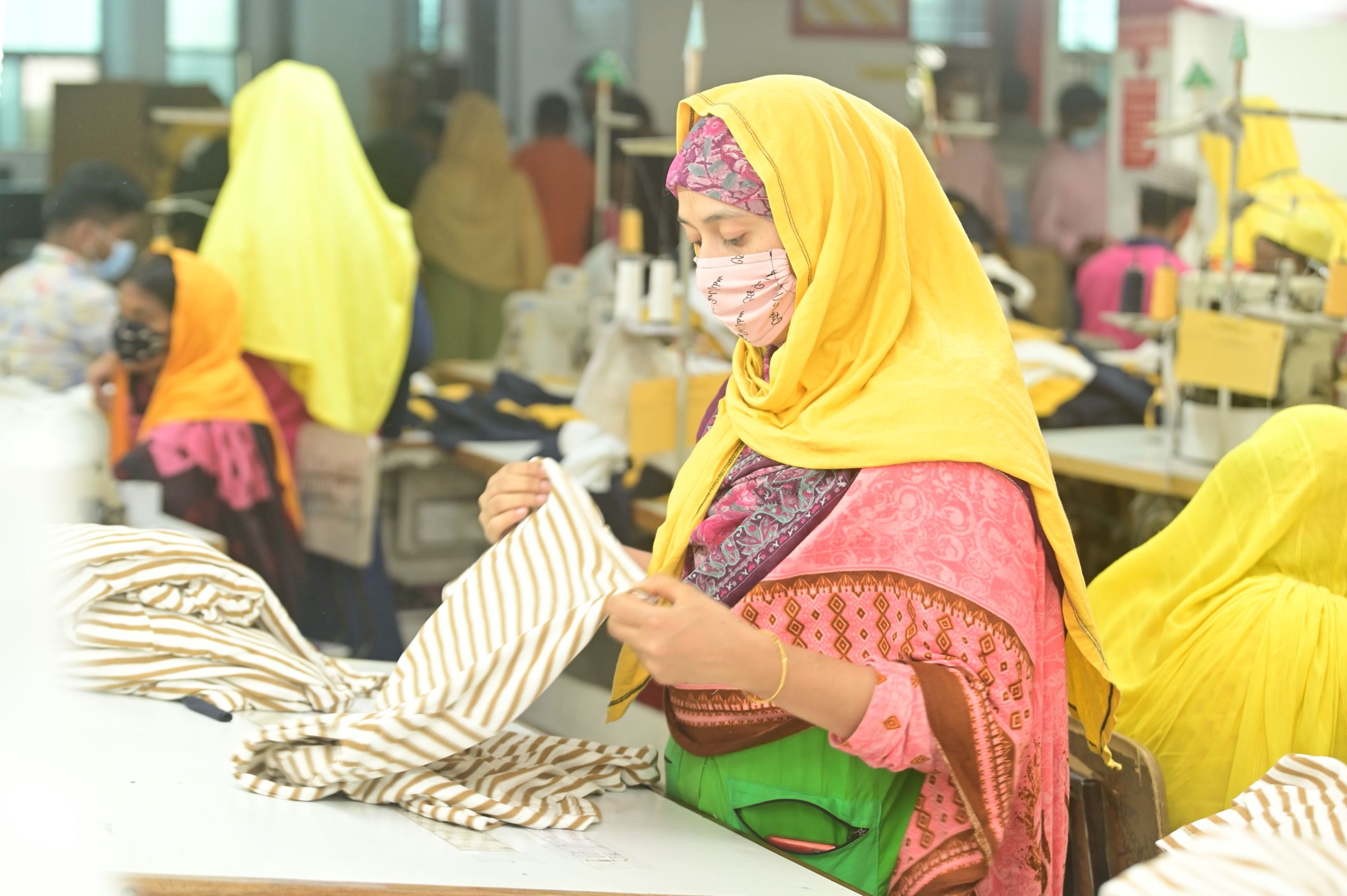
Kashimpur, Bangladesh – When 31-year-old day laborer Rani Akhter moved to the industrial city of Gazipur in central Bangladesh six years ago, she was pursuing a dream. She wanted a less physically arduous job than harvesting crops—and one that paid better. With economic stability, her 12-year-old son Abeer and 10-year-old daughter Ayesha might have options that were never available to her.
Akhter, the sole earner for her family, quickly found work at Hamza Textiles, one of the country’s leading garment manufacturers. “All I had to do was walk up to the factory’s front gate and ask for a job,” she remembered. The steady income has helped her provide for her family, just as she had hoped. But the pandemic jeopardized the life she worked so hard to create.
“We were all really scared at first when COVID-19 hit. We thought we would lose our jobs,” said Akhter. “But we are really thankful that even during lockdown, the government has allowed factories to remain open and we are able to feed our families. They recognize us as front-line workers.”
The contributions of factory workers like Akhter have helped transform Bangladesh into the world’s third-largest exporter of ready-made garments. The industry comprised 81 percent of Bangladesh’s total exports in the 2020-2021 fiscal year, according to data posted by the Bangladesh Garment Manufacturers and Exporters Association (BGMEA).
But COVID-19 has threatened the industry’s growth—as well as the livelihoods of over 4 million Bangladeshis, mostly women, who work in garment factories. Once the pandemic began, it had an immediate impact on 1,150 factories that reported $3.18 billion worth of order cancellations, according to the BGMEA. The decline in international orders and drop in exports led to layoffs or furloughs for over 1 million workers nationwide by April 2020.
To help modernize Bangladesh’s ready-made garment industry—and allow workers like Akhter and DBL’s 38,000 other employees to continue to expand their skills and provide for their families—IFC has committed a $22.70 million financing package to Hamza Textiles Limited, part of the DBL Group. The financing marks IFC’s first COVID-19 support in the ready-made garment sector and uses funds from the International Development Association’s Private Sector Window (PSW), set up to catalyze investment in low-income and fragile countries.
The support for Hamza Textiles Limited helps the company move closer to meeting fashion brands’ commitments to sustainability—including initiatives such as the United Nations’ Fashion Industry Charter for Climate Action, which has set the goal of net-zero emissions by 2050. Hamza Textiles is also working with Partnership for a Cleaner Textile (PaCT), the IFC-led program that helps Bangladesh’s textile sector incorporate cleaner production practices.
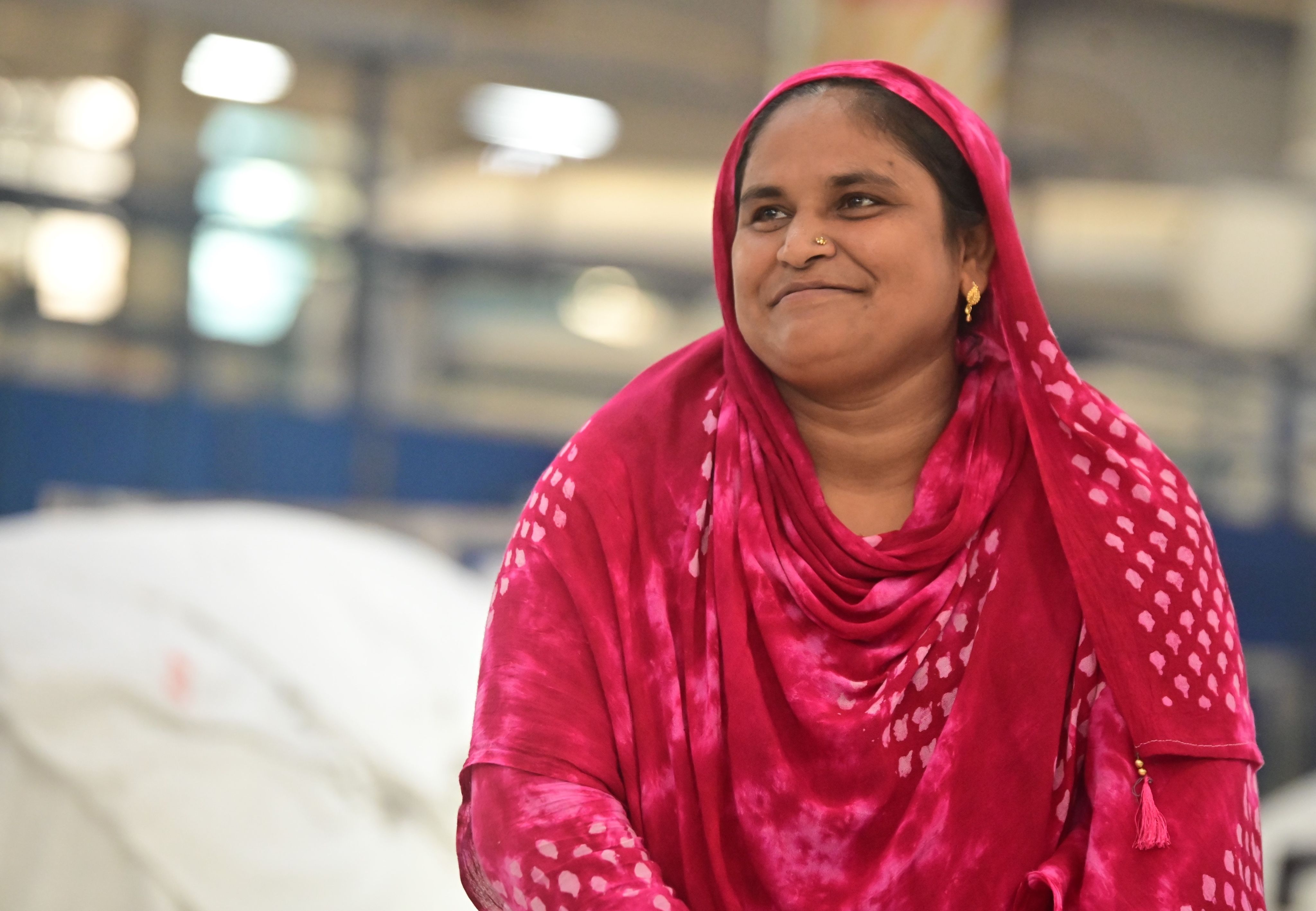
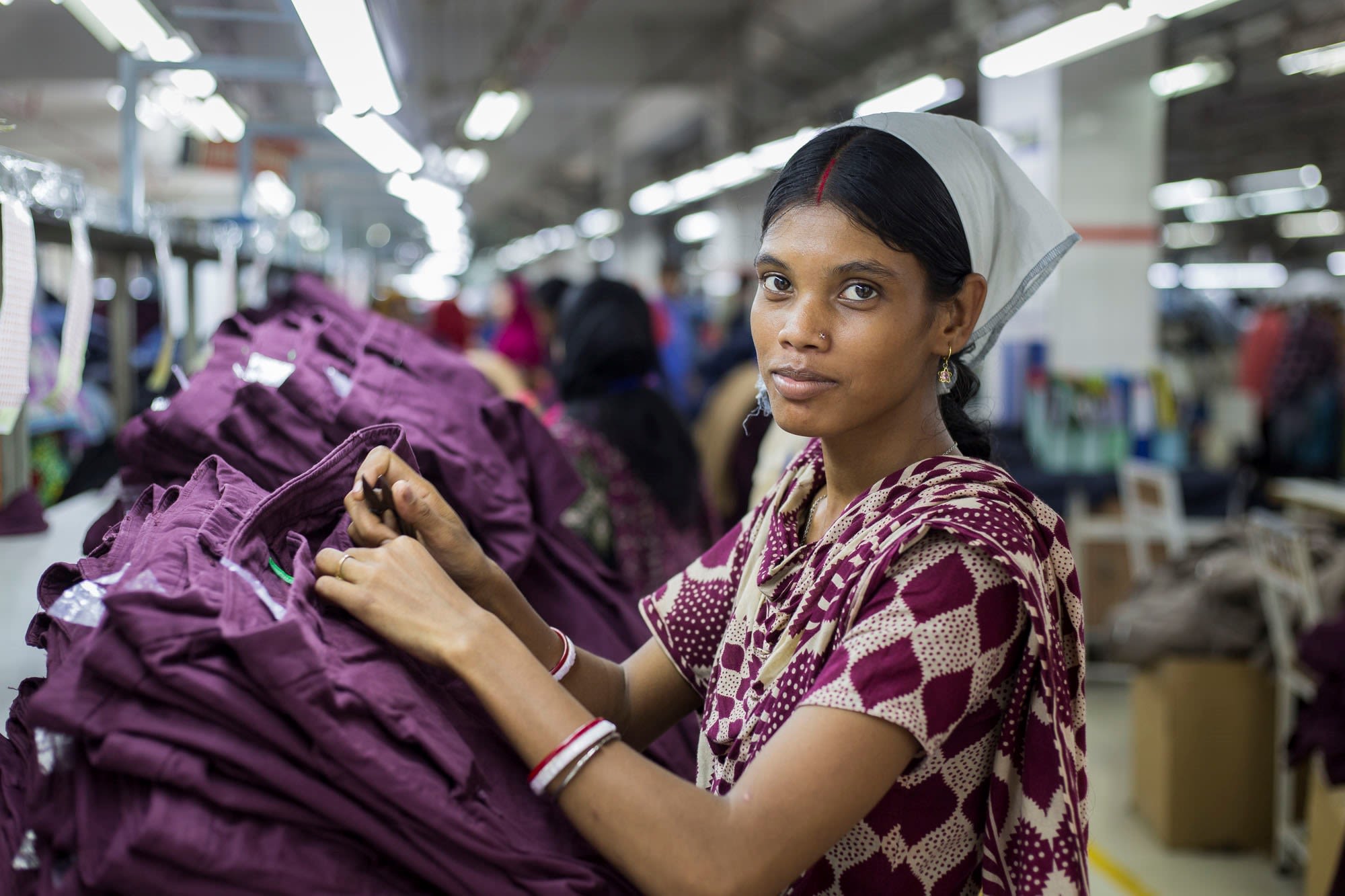
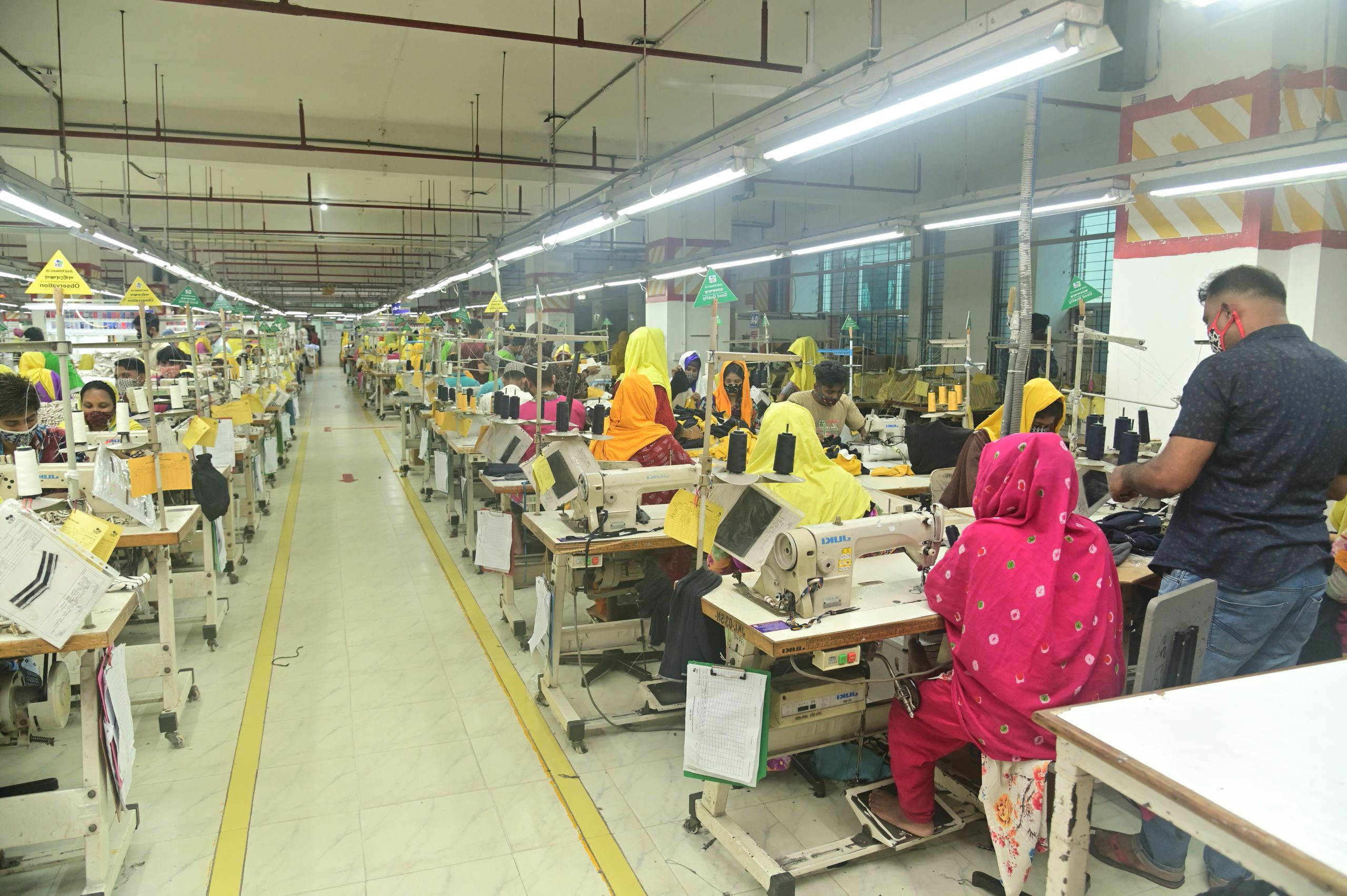
Integrating new technology and committing to sustainable practices is a significant part of boosting garment sector growth in Bangladesh. Rebounding from the COVID-19 pandemic and strengthening women’s employment is the other part.
Safety measures guided by the World Health Organization and Bangladesh’s government helped bring back most garment workers following lockdowns and furloughs. The Bangladesh Garment Manufacturers and Exporters Association, Bangladesh Knitwear Manufacturers and Exporters Association, and Better Work have also been supporting factories to help them remain open while looking out for employees’ well-being. Measures at Hamza Textiles include daily temperature checks, opportunities throughout the day to disinfect and wash hands, access to a doctor on the premises, and mask requirements. The company also uses online platforms for meetings, even among employees located in the factory, to avoid crowding, Rahman said.
Hamza Textiles will also participate in IFC’s Gender Equality and Returns (GEAR) program, which helps train women for supervisory roles and is jointly implemented by IFC and ILO as a Better Work training, funded by the European Union and Canada.
COVID-19 isn’t the only thing threatening to unravel the garment sector’s potential in Bangladesh, according to Joy Biswas, Senior Investment Officer at IFC.
“Even prior to COVID-19, Bangladesh’s ready-made garment industry was stagnating,” said Biswas. A lack of diversification among products and fabrics alongside slow adoption of technology were the main culprits, he said.
The installation of cutting-edge systems is one way to help factories get back on track. “There is significant scope to improve the manufacturing sector's performance and future prospects by promoting the adoption of better technologies in firms,” according to Siddharth Sharma, a World Bank Senior Economist. “As Bangladesh seeks to diversify its export base, move up the value chain, and create better-paying jobs, improving the productivity of firms remains central to the country’s manufacturing future,” he and coauthors wrote in a recent report.
With IFC’s backing, the company plans to set up a new factory with advanced and more efficient technologies, deepen its manufacturing base, and boost the country’s exports. Ultimately, Hamza’s improved operations are expected to contribute $8 million to Bangladesh's economy directly and indirectly by 2028, according to IFC estimates. About 900 positions for skilled workers may follow—with an additional $15 million that may be generated from employees’ earnings and opportunities for micro, small, and medium enterprises along the supply chain.
The stakes are high and the scope of ambition is significant, said Zahedur Rahman, Chief Operating Officer, Fabric Division at DBL Group, which owns Hamza Textiles and six other garment factories in Bangladesh. “We have to improve quality in a big way, [and] with this investment we will be able to overcome the challenges.”
Mr. Zahedur Rahman - Chief Operating Officer, DBL Group
Mr. Zahedur Rahman - Chief Operating Officer, DBL Group
Diversified and sustainable production meet demands
The DBL Group’s factories serve clients that are recognized around the world: global brands like H&M, C&A, Puma, Asda, Esprit, and Marks & Spencer, among others. Companies like those want to work with factories that can offer a one-stop solution for retailers—but just as important, they want their orders quickly so they can fulfill customers’ demand for the latest trends.
“Buyers’ lead time is decreasing so we have to act very fast” to produce and deliver garments, Rahman said. Doing that requires technology and processes that allow the company to manufacture its own fabric from synthetic fibers. Out of 4,500 ready-made garment companies in Bangladesh, only 10 percent have some fabric manufacturing capacity. A few companies, including DBL Group, have now started to invest in the systems that enable them to do this, so factories can quickly manufacture garments that are higher-quality and more complicated than a simple branded t-shirt or a pair of trousers. (About 85 percent of exports in Bangladesh come from low-value, basic garments.)
A modernized ready-made garment sector could help Bangladesh increase exports and support the country’s market diversification, encourage greater inflows of foreign direct investment and technology transfers, and help develop upstream and downstream industries.
Among consumers of fashion, sustainability is “becoming ever more important, with increasing consumer demand for environmentally friendly products, and concerns about climate change and social justice,” according to a recent report from McKinsey.
Those are not abstract concepts to Rahman, who reflects frequently on how to implement responsible manufacturing. “Whenever we talk about responsible manufacturing, it means that we need to believe in the philosophy of zero-emission, zero waste, and zero waiting,” Rahman said. “We are utilizing sunlight as much as possible. Our machines are consuming less water and less energy.”
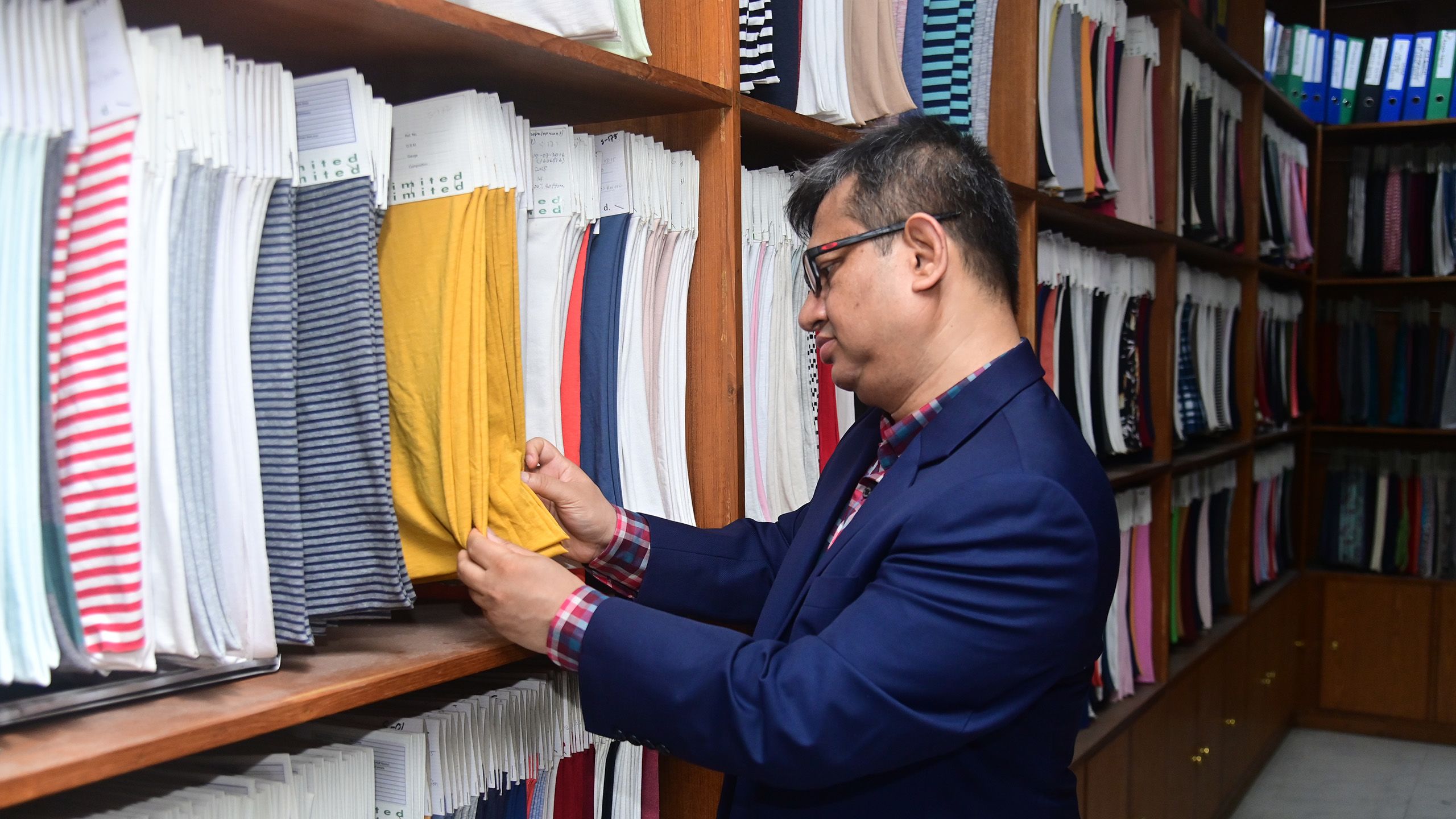
As part of its commitment to sustainable production, and participation in IFC’s Partnership for a Cleaner Textile (PaCT) program, which helps Bangladesh’s textile sector incorporate cleaner production practices, Hamza Textiles has invested $2.5 million in resource-efficient technology and management practices. This has resulted in a reduction of water and greenhouse gas emissions by 163,520 cubic meters per year and 26,109 tons of CO2 per year respectively between 2013 and 2019, according to an IFC assessment. Some of DBL’s other water-saving measures prevent local groundwater depletion and focus on community health, the company has said.
The initiatives are sources of pride for many Hamza Textile workers. “We have an ETP (Effluent Treatment Plant) facility in our factory,” said Mohammad Shimul, who works as a machine operator in Hamza’s washing department. “This allows us to deal with chemical waste and dyes in wastewater in an environmentally-friendly way. If we didn’t do this the wastewater would destroy crops for the people living nearby.”
Investing in the latest technologies for sustainable production can also lower manufacturing costs. The new Hamza Textiles factory, for example, will be LEED-certified (Leadership in Energy and Environmental Design) with new energy-efficient machinery. One of those is a machine critical to finishing garments. It has heat recovery features resulting in 20 percent thermal savings compared to older, more conventional machines.
Creating new career opportunities for women
The long-term health of the ready-made garment industry is critically important to women workers’ continued economic empowerment and social gains, according to research from the Subir and Malini Chowdhury Center for Bangladesh Studies at UC Berkeley. Women workers comprise 61 percent of all garment factory employees in Bangladesh. “The role of women in Bangladesh’s RMG [ready-made garment] industry cannot be overstated,” the report found. High numbers of employment among women have “enabled Bangladesh to have a significantly superior rate of female participation in the labor force, compared to its major South Asian neighbors.”
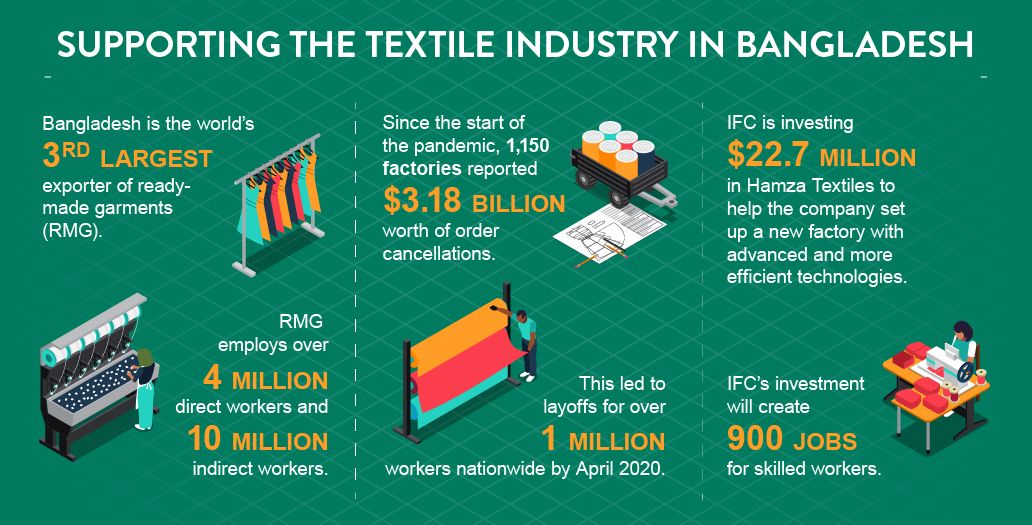
While women make up more than half of all workers in the sector, however, they continue to be overrepresented in lower-paid positions, with men holding the majority of supervisory roles, according to Better Work Bangladesh. That’s why skills and leadership training is key to their career progression.
Manju Khatun, a mother of two, experienced the benefits of skills training before COVID-19 hit. She became a supervisor at DBL Group in 2019 after attending a training program supported by IFC’s Gender Equality and Returns (GEAR) program. Her salary rose to 16,000 Bangladeshi taka (about $188) a month, higher than that of her husband, who also works at DBL.
It builds on a successful IFC-led pilot with Better Work Bangladesh that trained 144 female sewing operators and other workers in 28 factories. An assessment of the pilot showed that 60 percent of the trainees received a promotion offer within weeks of completing the training. The program also boosted corporate productivity: efficiency gains rose on average five percentage points on production lines led by trained supervisors.
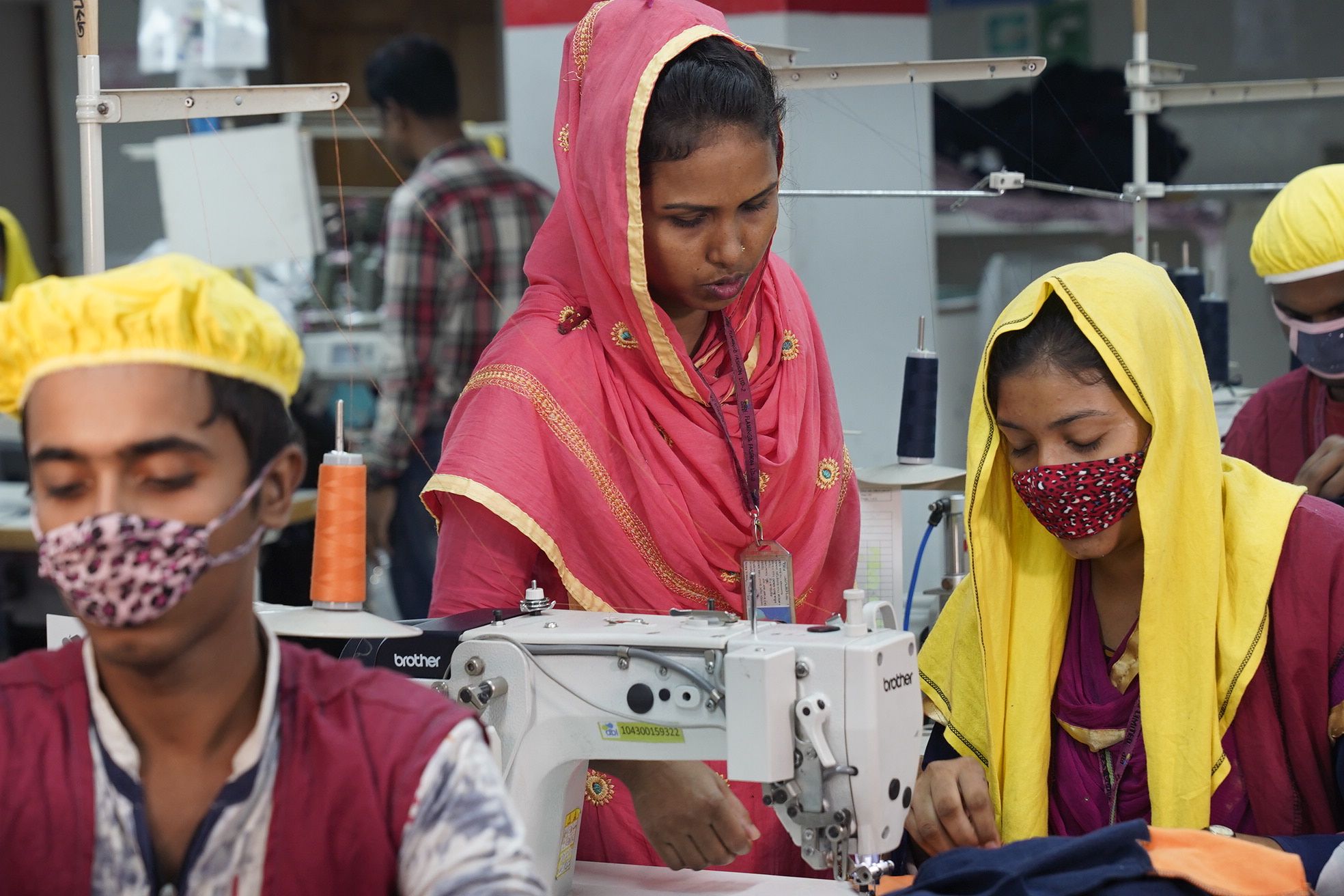
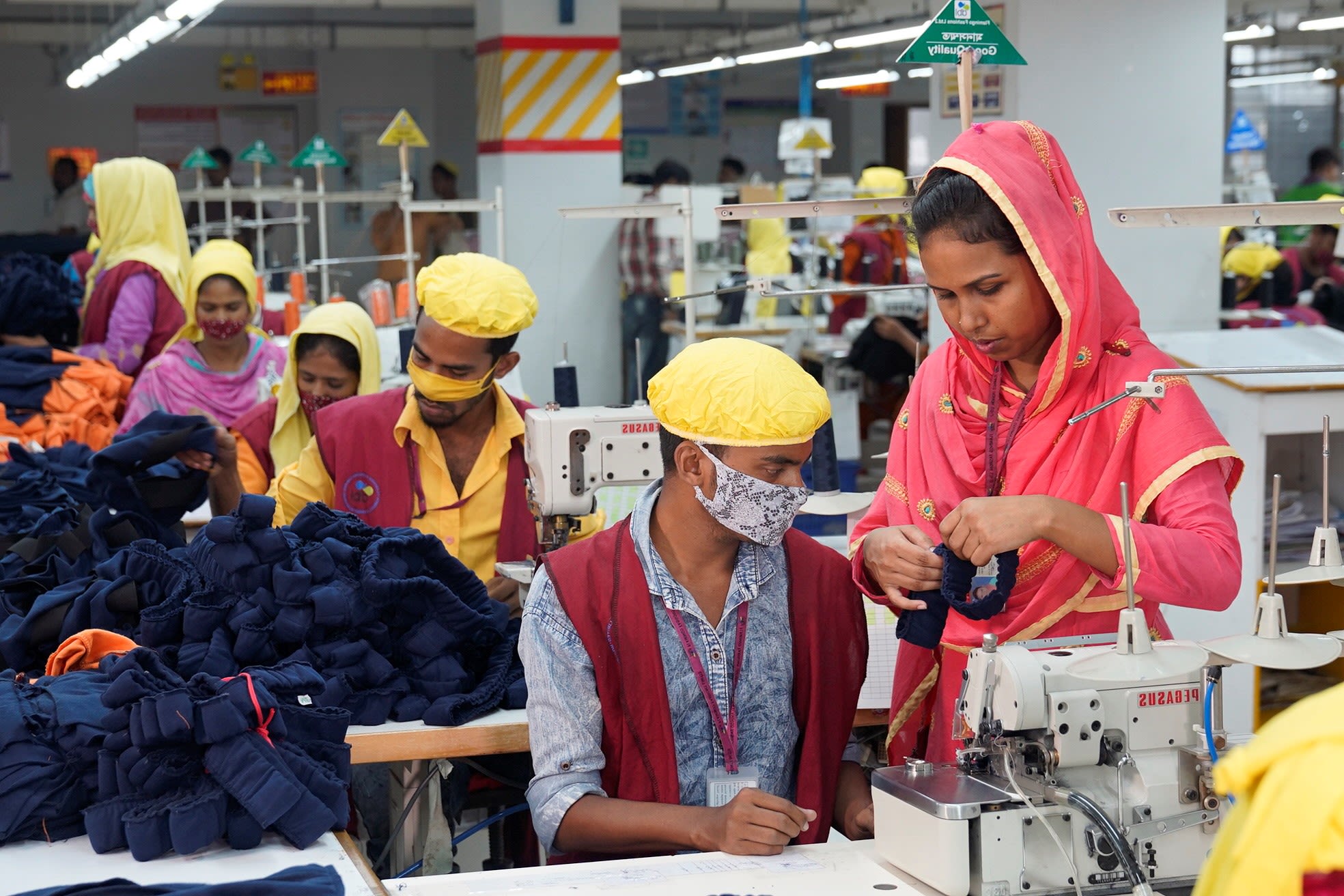
Although elevating women workers’ skills is “the right thing to do,” research from the International Labour Organization (ILO) confirms that “putting women in supervisory roles improves business performance and in-factory relationships,” said Conor Boyle, ILO’s Head of Programme Development and Country Programmes for Better Work. “In an ideal future, we are not ‘putting’ women in these roles, rather, women are rising and seizing leadership positions with the advent of a new skill set and opportunities made available to them.”
Rahman, from the DBL Group, has also seen that skills training for women workers in ready-made garment factories can strengthen the bottom line of the companies they work for. “We have to encourage more women to get technical skills and education, so they can get better employment and earn more,” he said. “I want to include not only gender diversity but also people having various kinds of disability that might limit them to come and work in our industry.”
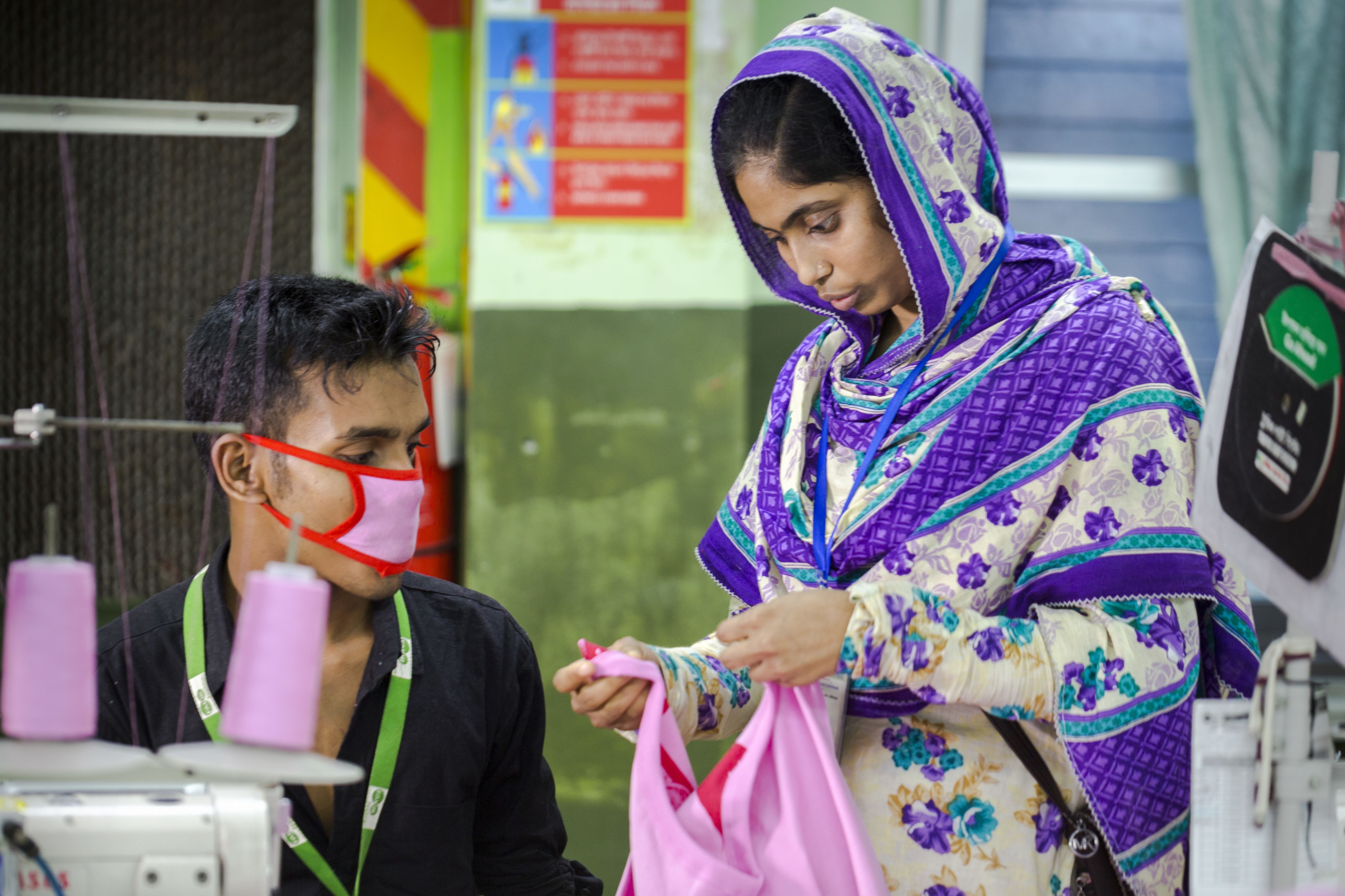
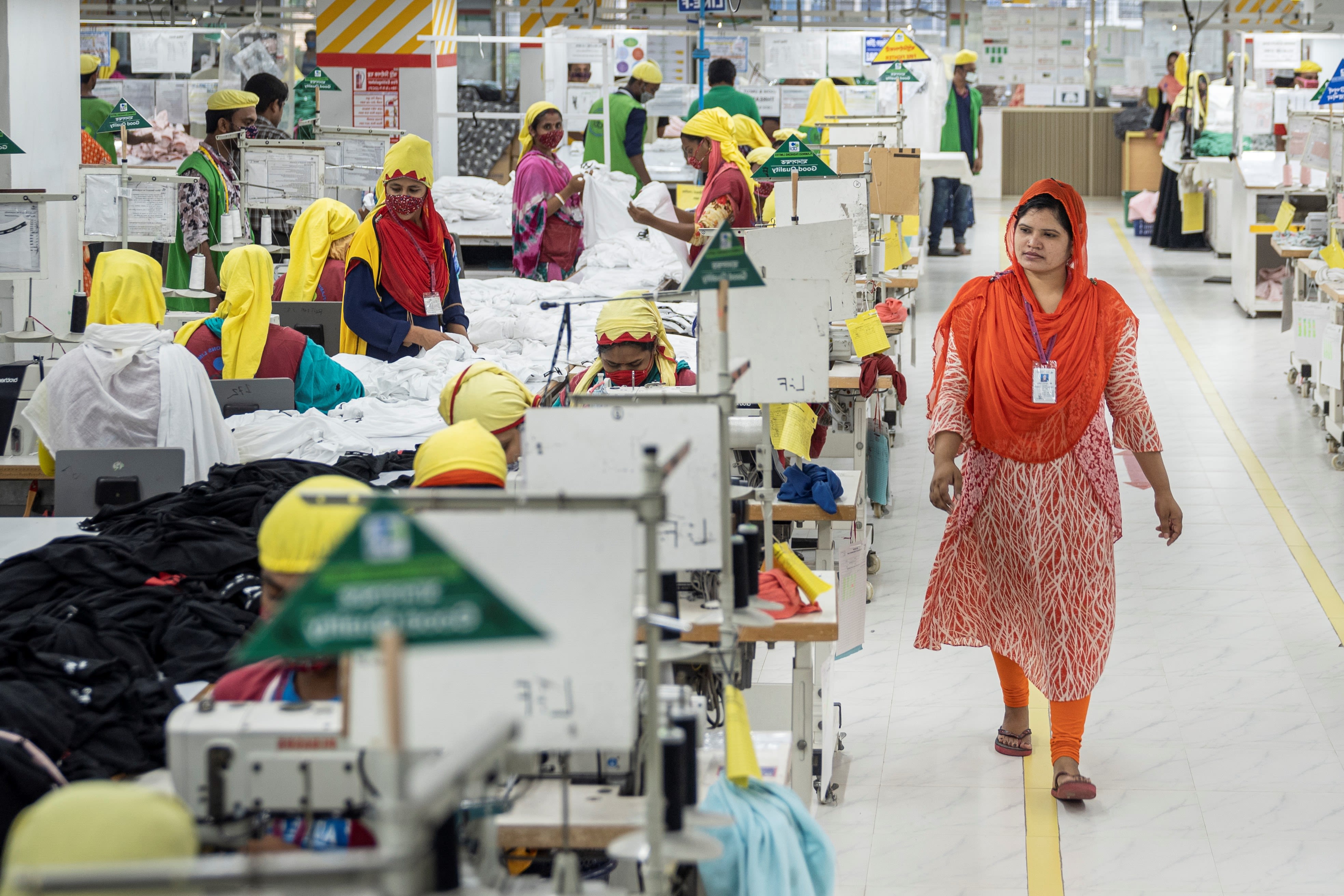
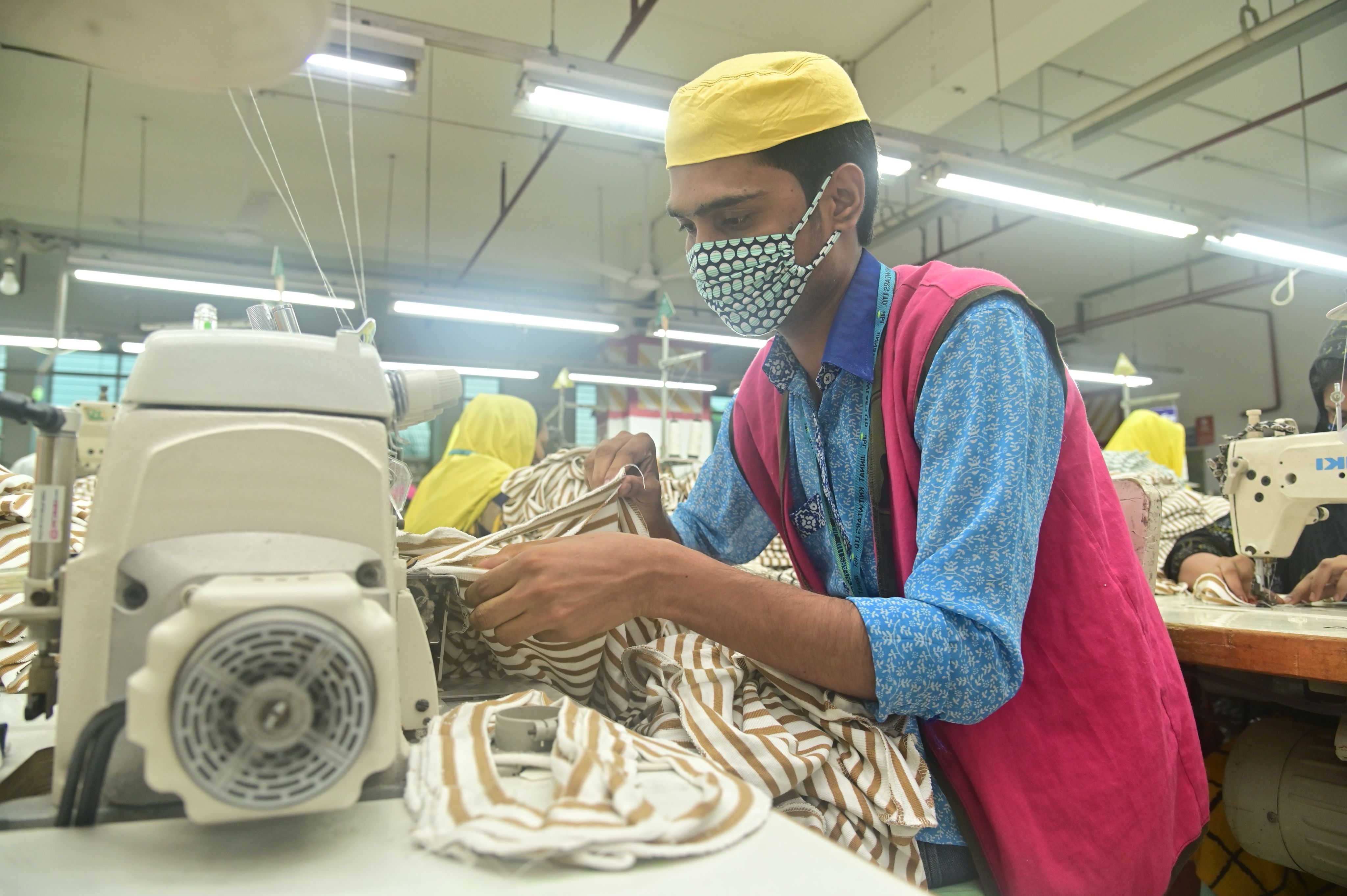